Sheet metal – it’s a familiar term, but what exactly is it and how is it used? Measuring as thin as 0.006″ and as thick as .25″, it’s a sheet of metal that can be used to create a wide array of products. These sheets can be made up of a variety of metals, including steel, copper, and bronze. For the purposes of HVAC systems, the most common metal types are aluminum and galvanized steel.
Sheet metal has many benefits in the application of ductwork, including being customizable to the exact needs of any HVAC project. At Custom Aire, our state-of-the-art fabrication shop and experienced team of experts allow us to provide exceptional custom ductwork that improves both the aesthetic and energy-efficiency of every commercial project we’re a part of. To learn more about how it’s made and the benefits it provides, keep reading.
Sheet Metal Fabrication Processes
When fabricating sheet metal for HVAC ductwork, there are two main processes it goes through: shaping and joining. Even a cursory glance at a network of HVAC ducts can tell you that there is a wide range of shapes the pieces can take, and many ways in which they can be joined.
Shaping
The two types of shaping that sheet metal must undergo during the fabrication process are called forming and cutting. Here are some of the most common methods, their associated applications, and the tools to accomplish each.
Forming
- Rolling creates spiral ductwork by sending the sheet metal through a roller
- Bending folds metal into angles typically found in box ductwork and plenums, by using a press brake
- Stamping impresses a shape or other design into the metal with a die
- Stretching makes contours in the sheet metal by pulling it over a stretch press and die
Cutting
- Shearing cuts across a flat sheet to make the metal piece into the preferred size, using shearing blades
- Blanking punches a hole into the metal to produce pieces of a desired shape, using a blanking die
- Laser, plasma, or waterjet cutting make highly detailed precision cuts in the metal sheet using beams of light, gas, or water
Joining
After the pieces have been shaped, they are ready for the last part of the fabrication process, which is joining. Just as with shaping, there are several methods used in the joining of sheet metal for HVAC systems.
- Welding is ideal for airtight applications such as ductwork
- Rivets are a permanent means of fastening sections together
- Flanges hold sections strongly and securely in place
- Folding and Tab Joints work like a buckle to fit different metals together
Now that we’ve explored the fabrication processes of sheet metal, let’s look at why it has become the preferred material for commercial HVAC projects.
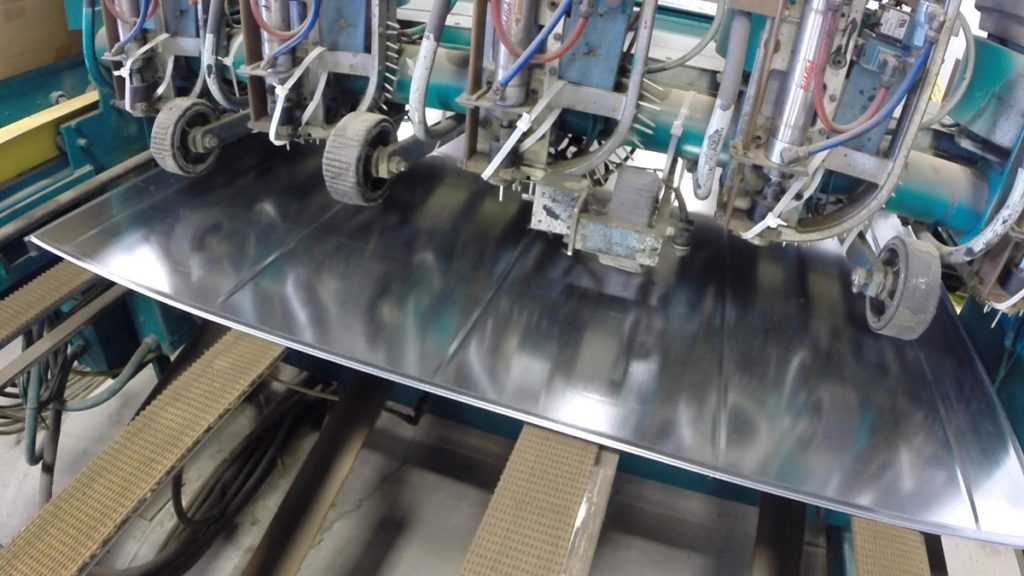
Benefits of Sheet Metal
There are numerous benefits to using sheet metal in the fabrication of HVAC ductwork, including:
Custom Fabrication
No two HVAC systems are exactly alike. Sheet metal ductwork has to be made specifically for the space it’s going to serve. Custom-made air ducts with precise shaping and joining helps to keep air from leaking out, thanks to the rigidity of the metal and the skills of the fabrication team. At Custom Aire, we design and build custom ductwork in our own fabrication shop, ensuring that the network of ducts in your commercial space provides seamless, leak-free airflow.
Energy-Efficiency
A perfect fit means your HVAC system doesn’t have to work as hard to get air through your building. With custom-fabricated sheet metal ductwork, there are no gaps for the air to escape. The airflow will be directed where it is intended to go, arriving at its destinations more quickly and efficiently. Of the many ways to achieve energy efficiency in your commercial building, airtight ductwork is one of the longest-lasting. It’s better for the environment and better for your bottom line.
Easier to Maintain
Because sheet metal is more durable than other traditional HVAC materials, it lasts longer than such materials as PVC and fiberboard, which can sag over time and even become structurally compromised with necessary regular cleaning. Sheet metal is easier to clean, as it doesn’t have crevices where dust can hide, and isn’t prone to tearing, as fiberboard’s foil covering would be. The energy-efficient nature of sheet metal ductwork also adds longevity to the heating and cooling units, making it easier to stick to a regular maintenance schedule.
At Custom Aire, we take pride in producing sheet metal ductwork of the highest quality for commercial projects of any size and industry. Contact us today to learn more about how custom sheet metal fabrication can make a difference in your project.
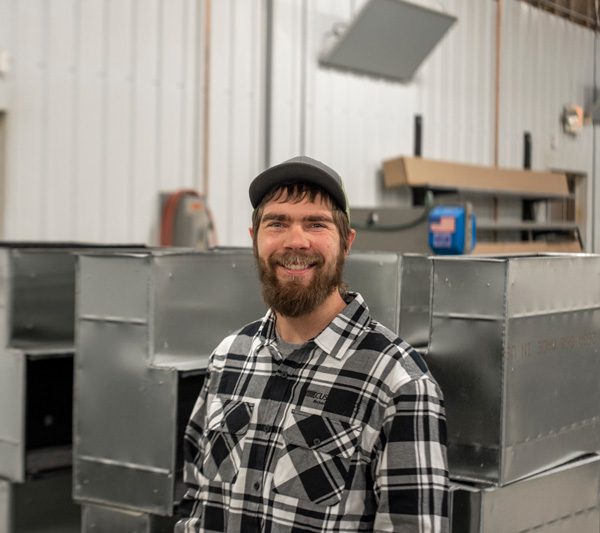